Balancing human-automation level in the human-robot collaborated assembly lines
- VF-KDO communication
- Sep 28, 2021
- 2 min read
In light of the Industry 5.0 trend towards human-centric and resilient industries, human-robot collaboration (HRC) assembly lines can be used to enhance productivity and workers’ well-being – provided that the optimal allocation of tasks and available resources among stations known as assembly line balancing problem (ALBP) can be determined. This study is driven by the need to solve the more complex ALBP found in advanced manufacturing systems where humans and collaborative robots share the same workplace and can simultaneously perform tasks in parallel or in collaboration (ALBP-HRC).
In-line with the Industry 4.0 techno-economic vision, the design of assembly lines in industries has shifted from the traditional configuration, namely either manual or robotic, towards human-robot collaboration (HRC) configurations, so as to achieve both higher productivity and flexibility. Figure 1 shows the 3D layouts of an assembly line with (a) manual, (b) robotic, and (c) HRC environments.
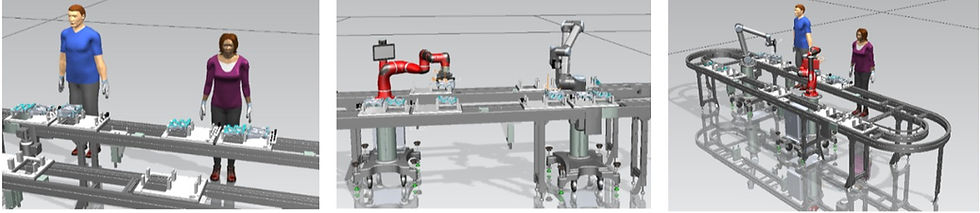
To make all HRC advantages attainable, the ALBP-HRC with real-world challenges found in automotive industry as shown in Figure 2(a) has been formulated as a new Mixed-integer programming (MIP) and solved using GAMS (General Algebraic Modeling System) software. The obtained solution for ALBP-HRC is shown in Figure 2(b), where the optimal balance and schedule of tasks and resources (both humans and robots) among stations are determined.

Furthermore, a novel neighborhood-search-based simulated annealing (SA) algorithm is highly customized to efficiently solve larger ALBP-HRC with higher complexity. Different variants of this SA algorithm incorporating random, variable, and adaptive neighborhood selections are developed and compared with the MIP model. The computational study shows that the adaptive SA produces promising solutions relative to the MIP, while dominating the other variants of the SA algorithm for real-world cases and different test problems. Moreover, depending on the problem characteristics, the results indicate that by using HRC with multiple humans and robots at stations, the productivity of assembly lines could be increased up to 52%.
Authors: Amir Nourmohammadi (Research Assistant), Amos Ng (Professor of Automation Engineering) and Sunith Bandaru (Associate Professor of Production Engineering), University of Skövde.
Comments